Así se fabrica un casco de carreras
Airoh, referencia absoluta en el ‘off road’ (118 Mundiales), abre las puertas de su fábrica a AS y muestra el trabajo artesanal que conlleva la protección más importante.
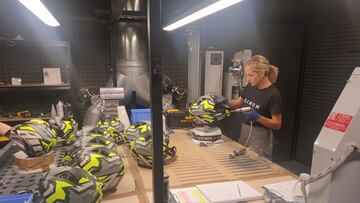
Airoh, marca de referencia absoluta de cascos en el mundo del ‘off road’, protegiendo la cabeza de leyendas como Tony Cairoli o la gran estrella española del motocross, Jorge Prado, también está en la velocidad y gusta mucho ahora su modelo GP550S. Lo usan ya pilotos como María Herrera en la Copa del Mundo de MotoE o David Alonso, el campeón de la Red Bull Rookies, además de otras promesas italianas. La fábrica transalpina, que produce 300.000 cascos al año, ha abierto a AS las puertas de sus instalaciones, en Bergamo, para mostrar el trabajo artesanal que conlleva la protección más importante del piloto y comprobar en boca de su fundador en 1997, Antonio Locatelli, lo que le mueve a dar este salto al asfalto: “La pasión”.
El departamento de investigación y desarrollo, de producción, la galería del viento, el almacén y las oficinas de marketing lo componen en Airoh alrededor de 80 personas y todo se encuentra en un mismo edificio, situado en Bergamo, a pocos kilómetros de Milan. El proceso de fabricación está muy bien estructurado con diversas cadenas de montaje y es fácil de entender en la visita guiada por la hacienda que ofrecieron a este diario Roberto Pagnanini y Federica Colpani.
1. Departamento de diseño
Un grupo de ingenieros trabajan en el departamento de diseño de Airoh y cada modelo obliga desde que nace la idea en este departamento hasta su producción final una media de 18 meses de trabajo.
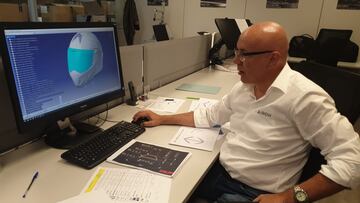
2. Maqueta de escayola
Una vez diseñado el casco, lo primero que se hace es una maqueta a mano en escayola, con todas las piezas del casco, que lleva 100 referencias con las que a continuación se hace un producto matemático.
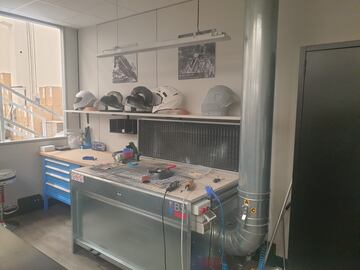
3. El escáner
¿Cómo se convierte una maqueta en un producto matemático? Con un escáner, tras el cual se imprime el casco en 3D para llevarlo a continuación al túnel del viento.
4. El túnel del viento
El túnel del viento mide principalmente la resistencia al aire u funciona a base de prueba-error hasta que deja de dar fallo a nivel aerodinámico. El túnel del viento de Airoh es de última generación, cuentan con él desde 2018, dispone de 30 sensores para medir temperaturas y movimientos, llega hasta los 40 grados y sopla hasta los 200 kilómetros por hora. En él se miden los kilos sobre la cabeza que soporta el casco y si no da casi nada, como así sucede con los modelos que pasan a fabricación, es que funciona bien aerodinámicamente. Según el operario que había en el túnel durante la visita de este diario, generalmente se necesitan tres meses por diseño y por talla para dar luz verde al casco de turno.
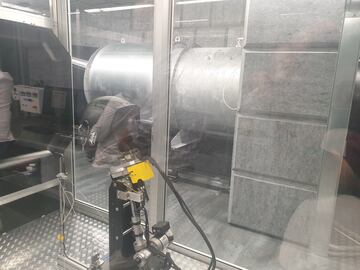
5. Tallaje
Airoh dispone de tres calotas y cinco tallas en su casco tope de gama, el GP550S. La calota más pequeña es para la talla XS, la mediada para las tallas S y M y la grande para la L y XL. Para hacer dos tallas diferentes de una misma calota lo que se hace es variar la espuma interior.
6. Líneas de producción
Hay dos líneas de producción, una para trabajar con la fibra y el carbono y otra para trabajar con el plástico, aunque puede variar porque hay cascos menos complicados que otros.
A. Control de calidad de la calota y la pintura. Trabajo visual y a mano.
B. El casco pasa a la habitación de ambiente controlado, donde dos operarias evitan que haya suciedad en el casco y comienzan el montaje, agujereando, limando, aspirando y colocando tornillos. Estas operarias trabajan un máximo de cinco calotas por hora y no es casualidad que sean mujeres en vez de hombres, algo que prima en todo el proceso, porque se busca una mano hábil y más pequeña.
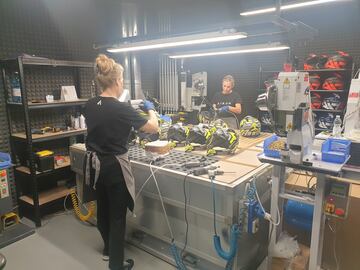
C. Cadena de montaje. Se ponen las gomas con pegamentos y el tirador del casco. Es un proceso delicado y Airoh saca pecho por haber sido la primera marca en el mundo en a la calle con la homologación ECE 22 06, lo que hizo con dos modelos off road. En la cadena de montaje se incluye también la estructura interna y el sistema de cierre, que incluye un código QR que da la historia del casco. Por último, se introduce el almohadillado, se etiqueta y se envasa para ser trasladado al almacén.
7. Test de homologación y producción
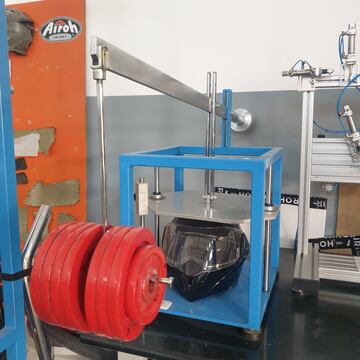
Cada 3.200 cascos se testa un modelo. La filosofía de Airoh va más allá de cumplir con la homologación y trabaja con un par de universidades para entender lo que pasa en la cabeza de una persona cuando hay un impacto. En los cascos actuales, hay 17 puntos de impacto que se testan. Con la ECE 22 05 eran sólo cinco puntos, pero con la introducción de la ECE 22 06, a partir de enero de 2021, son como mínimo 12 más para un total de 17, pudiendo haber puntos adicionales. Y todos ellos se comprueban con 15 tipos de test diferentes, con cabezas de mentira, de diversas tallas y pesos, en los que se verifica todo lo verificable con simulaciones a 50 por hora, obteniéndose los datos en proporción a esa referencia.
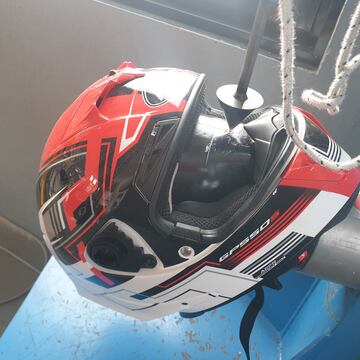
Y así es como fabrica un casco de carreras una marca que de carreras sabe un rato, porque son ya 118 títulos mundiales conquistados por Airoh en el mundo de la tierra, motocross y enduro principalmente, que ya tiene títulos en el asfalto (de 125cc y Supersport), y que aspira a ser también algún día referencia en el Mundial. Buena suerte y la mejor de la protección para todos.